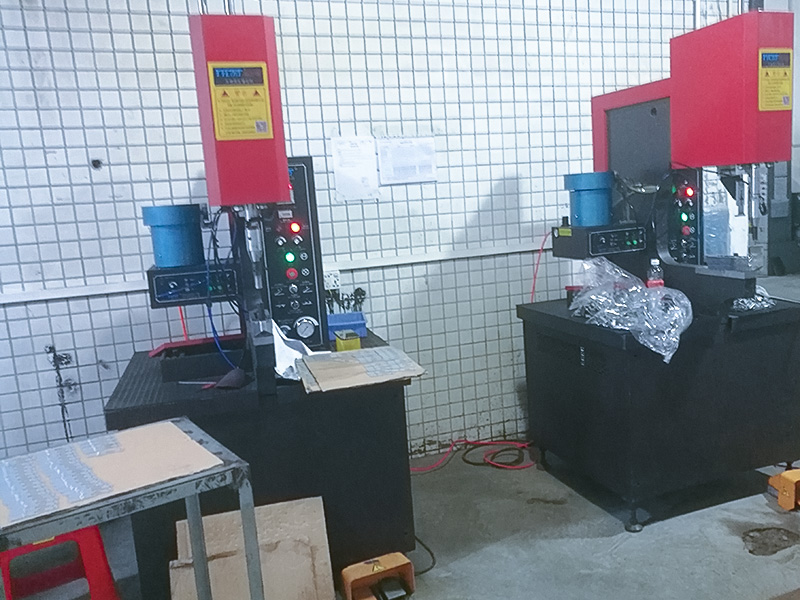
Four basic cold processing links to optimize sheet metal design
-
by Yan yifan
- 516
Generally, sheet metal parts have obvious advantages in strength, weight and cost, and have better point-to-point performance than traditional parts. Therefore, up to now, sheet metal parts have been gradually applied in China’s high-tech fields such as electronics and communication. At the same time, people have gradually put forward higher requirements for the quality and function of sheet metal parts, The proper optimization of the original sheet metal processing technology has become the focus of sheet metal processing personnel. According to the actual research, this paper believes that the optimization of processing technology should be carried out one by one from the application of four basic cold processing links of sheet metal processing.
1 blanking link
First of all, as far as the blanking link is concerned, generally speaking, blanking refers to the separation of sheet metal materials through the stamping of the die, so as to realize the separation of sheet metal. This link is usually applied to the processing of parts with relatively simple processing shape, so as to achieve a high degree of accuracy of processing shape and minimize the waste of materials. In this link, first of all, the shape of the blanking sheet metal parts should be controlled. In the corner area of the outer and inner holes of the blanking, an arc should be set to excessive the corner, so as to avoid sharp angle and reduce the problem of mold cracking caused by improper subsequent heat treatment, which will affect the subsequent sheet metal construction; Then, the punching and its minimum value should be optimized. Usually, when punching sheet metal parts, if the punching size of the punched sheet metal parts is small, the load on the punch will be reduced to a great extent. However, if it is too small, it is easy to cause the data of the pressure carried by the die to suddenly become more, which will affect the quality of the actual die. For example, in this link, the punching of sheet metal parts should be set according to different load targets of sheet metal parts. In the basic state, the length of the hole diameter should be more than twice the hole spacing and greater than 3.00mm. Finally, the cantilever and groove on the blanking part should be set to avoid being too narrow or too long in the actual process application link, so as to improve the strength of the relevant die edge and control the notch width of the cantilever to be greater than 200 sheet metal thickness.
2 bending link
Bending link usually refers to the process of preventing the sheet metal material on the bending equipment, causing the elastic deformation of the sheet metal material through the pressure of the upper die or the lower die, and plastic deformation according to the actual design scheme after the elastic deformation. In the application process of this link, we should select different parts and set sizes according to the actual design requirements, and determine the actual operation of bending according to the thickness of sheet metal raw materials. According to the actual bending experience, local abnormal deformation is most likely to occur in the bending link, which will affect the appearance quality and practical application of sheet metal parts. Therefore, in the actual operation link, if you want to optimize the process for the bending link, the operator should cut in advance according to the actual situation, so as to avoid the problem of subsequent deformation. At the same time, when the parts need to be bent for many times, a comprehensive estimation should be made in all the bending operation links to avoid the previous bending operation affecting the subsequent bending process, so as to achieve the expected design goal of sheet metal parts.
Rackmount Storage Enclosure | Jbod Storage Enclosure | Storage Server Chassis
3 press riveting link
The press riveting link of sheet metal parts refers to the deformation of sheet metal materials through the action of pressure, so as to couple them together. This process is usually applied to screw press riveting, bolt press riveting and other links. As for the end press riveting operation link, the nut is usually circular and has an embossed gear and wire notch. Therefore, for the press riveting link of sheet metal parts, not only the quality of the original nut manufacturing link is optimized, but also the welding work is avoided. If you want to gain a better design scheme, first of all, you can select different specifications of molds according to the height of different pressed bolts in the actual press riveting link, and adjust the pressure release of the press riveting device to ensure the pressing quality of nuts and avoid the problem of waste parts at the same time. Secondly, the appropriate sheet metal size can be selected in the setting of press riveting structure, so as to ensure the results of press riveting and avoid the falling out of the pressing link of sheet metal parts.
4 welding link
Welding link is one of the important ways to connect all parts of the structure together in the cold working link in the whole sheet metal processing process. Therefore, usually, this link will be operated under the background of high temperature. At present, most of the common welding methods are carried out by argon arc welding, contact spot welding and so on. Therefore, in the actual welding link, different welding methods should be selected according to the properties of different sheet metal parts, so as to reduce the welding deformation to the greatest extent and improve the actual efficiency of welding. For example, in the actual welding link, first of all, sufficient welding control should be determined. Secondly, the length of the welding part needs to be controlled more accurately to avoid the deformation of the sheet metal and optimize the load of the welding point at the same time.
QUICK LINKS: FAQ | Switch Mounting Bracket | Aluminum Rack Panels | Racing Lawn Mower Parts | CNC Stamping Parts | OEM Custom Radiator Support Bracket | Custom Metal Fabrication |TV Back Panel| Custom Rackmount PC | Sheet Metal Enclosure Fabrication | Metal cases Aluminum case suppliers
Generally, sheet metal parts have obvious advantages in strength, weight and cost, and have better point-to-point performance than traditional parts. Therefore, up to now, sheet metal parts have been gradually applied in China’s high-tech fields such as electronics and communication. At the same time, people have gradually put forward higher requirements for the quality and…
Generally, sheet metal parts have obvious advantages in strength, weight and cost, and have better point-to-point performance than traditional parts. Therefore, up to now, sheet metal parts have been gradually applied in China’s high-tech fields such as electronics and communication. At the same time, people have gradually put forward higher requirements for the quality and…