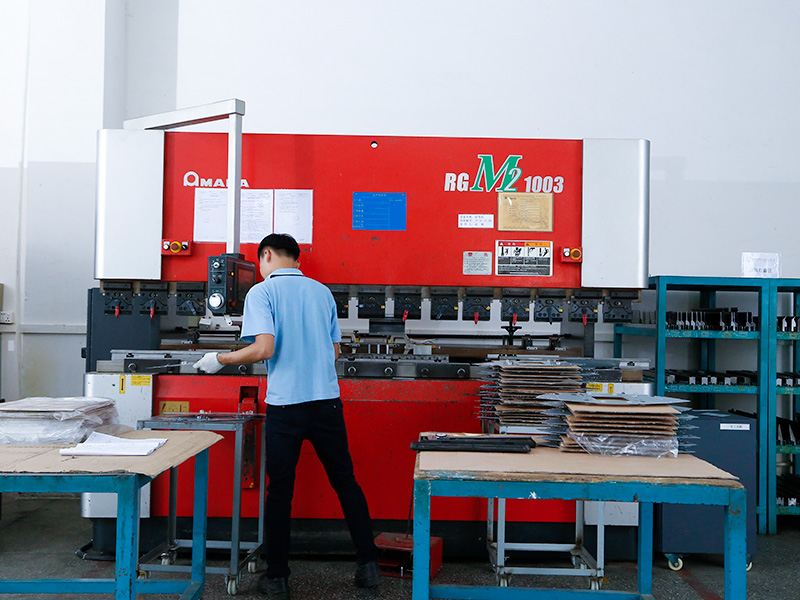
Bending problems to be considered in sheet metal design
-
by Yan yifan
- 433
The design needs to consider what is processing before forming and what is processing after forming. Considering that in the process of work production, some holes must be bent first and then processed: round holes, square holes, waist round holes, threads, etc. close to the bending edge need to be processed during blanking. If the blanking is carried out directly, it cannot be completed in subsequent processing. The waist circle will pull holes during bending, and the threaded holes cannot be tapped with common taps. The design needs to consider which can be formed by sheet metal and which can not be formed by sheet metal.
Consider whether the machine tool can be directly used for positioning. If not, reserve two small squares for positioning and remove them after bending. Consider the bending direction of sheet metal: especially the bending of non-ferrous metals, such as aluminum plate and copper plate. Depending on the texture direction of material rolling, bend perpendicular to the texture direction, not parallel to the rolling texture direction, which is easy to have bending cracks.
To reserve bending avoidance clearance: when the sheet metal bends the edge wrapped sheet metal part, the two bending surfaces have the relationship between the edge wrapped and the edge wrapped. When making the expansion drawing, draw the bending avoidance gap. Because when bending to 90 degrees, the sheet metal has bending spring back. In order to avoid less than 90 degrees after spring back, it is necessary to bend more than 90 degrees to offset the spring back. Therefore, the clearance shall be reserved for bending rebound avoidance.
Sheet Metal Frame | China Sheet Metal Manufacturer | CNC Sheet Metal
Cumulative error of multiple bending of sheet metal: the bending accuracy of sheet metal is not very high, which is generally controlled within 0.2mm. The higher the bending height, the lower the bending accuracy. When there are installation holes, threaded holes, riveting screws and riveting nuts on the bending surface, the cumulative processing error shall be fully considered. Increase the installation through hole or design the installation hole as waist hole to avoid installation error. Convenient for subsequent installation.
Consider the problem that the distance between the hole and the bending edge of sheet metal rivet screw or rivet nut is too small: during bending, there are bending deformation and tensile deformation at the same time. Holes and notches are too small from the bending edge, which will cause tensile deformation of holes and notches. Generally, there will be no bending deformation when the thickness away from the bending edge is 4.5 times of the material thickness.
The above is the problem that sheet metal bending needs to be considered in sheet metal design. Sheet metal design needs to fully consider the bending process and understand the bending process. The design is to be processed into products. The limitations of the sheet metal bending process cannot be ignored.
QUICK LINKS: FAQ |Custom aluminium enclosure | Sheet Metal Cover | Laser Cut Sheet Metal Cost | OEM Custom Radiator Support Bracket | Electronics case | Wholesale Sheet Metal | Metal Frames | Sheet Metal Chassis | Metal Manufacturing in China |
The design needs to consider what is processing before forming and what is processing after forming. Considering that in the process of work production, some holes must be bent first and then processed: round holes, square holes, waist round holes, threads, etc. close to the bending edge need to be processed during blanking. If the…
The design needs to consider what is processing before forming and what is processing after forming. Considering that in the process of work production, some holes must be bent first and then processed: round holes, square holes, waist round holes, threads, etc. close to the bending edge need to be processed during blanking. If the…