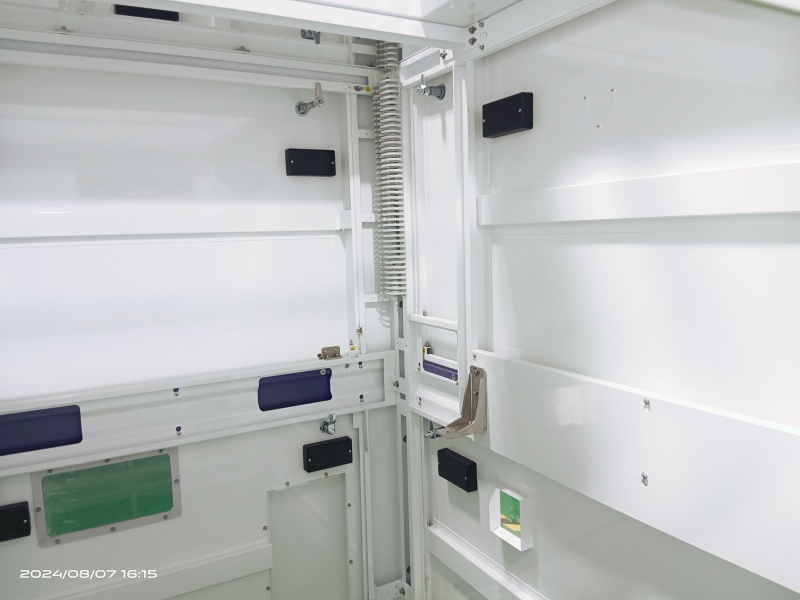
What is the process of sheet metal production?
-
by Jiatong
- 556
Sheet metal fabrication involves various processes to transform flat sheets of metal into desired shapes and components. These processes range from cutting and bending to assembling and finishing. Here are the main sheet metal fabrication processes:
1. Cutting
Shearing: This is a basic cutting method where a sheet is cut into straight lines using shear force, often with a guillotine-style machine.
Laser Cutting: Uses a high-powered laser to cut intricate shapes with precision. This method is efficient for complex designs and offers a clean cut.
Plasma Cutting: Involves using a plasma torch to cut through conductive metals like steel, aluminum, and brass. Plasma cutting is fast and suitable for thick metal sheets.
Water Jet Cutting: A highly accurate process that uses a high-pressure jet of water, sometimes mixed with abrasive particles, to cut through sheet metal without generating heat. This is ideal for heat-sensitive materials.
2. Punching
Punching involves using a punch and die to create holes or cutouts in the sheet metal. It is commonly used to produce specific shapes or patterns in the metal by forcing it through the die with a punch.
CNC Punching: Computer-controlled punching machines (CNC) allow for precise and automated hole placement, often used for mass production.
3. Bending
Press Brake Bending: A press brake machine is used to bend sheet metal into a desired angle or shape. The sheet is placed between a punch and a die, and pressure is applied to create the bend.
Roll Bending: Sheet metal is passed through a series of rollers to form cylindrical or curved shapes.
Folding: Similar to bending but uses a specialized machine to fold the edges of sheet metal for applications like boxes or enclosures.
4. Stamping
Stamping involves pressing the sheet metal between a die and a punch to form specific shapes, patterns, or indentations. It is commonly used to produce high-volume components like automotive parts.
Deep Drawing: A specific stamping process where the sheet metal is drawn into a cavity to create deep, hollow shapes. This method is often used for producing items like cans or enclosures.
5. Forming
Roll Forming: In roll forming, continuous bending of long strips of metal takes place through consecutive sets of rollers. This process is used to create long components with uniform cross-sections, such as metal roofing panels.
Spinning: The metal is rotated at high speeds while a tool shapes it, often used to create symmetrical, round objects like funnels or cones.
Stretch Forming: The sheet metal is stretched and bent simultaneously over a die to create large, curved surfaces, often used in aerospace applications.
6. Welding
MIG and TIG Welding: Various welding techniques are used to join sheet metal components together. MIG (Metal Inert Gas) welding is faster and used for thicker metals, while TIG (Tungsten Inert Gas) welding is more precise and suitable for thinner metals.
Spot Welding: A resistance welding process used to join two or more metal sheets at specific points by applying pressure and an electric current.
Seam Welding: A continuous welding process where rollers are used to apply pressure and current along the seam of two overlapping metal sheets.
7. Assembling
Riveting: Mechanical fasteners, such as rivets, are used to join two or more sheets of metal. Riveting is common in industries like aviation and construction.
Bolting and Screwing: Threaded fasteners are used to assemble sheet metal components, allowing for disassembly and maintenance when necessary.
Adhesive Bonding: Special adhesives can be used to bond metal sheets together, offering a smooth surface finish and avoiding the need for heat or fasteners.
8. Embossing and Engraving
Embossing: The process of creating raised designs or textures on the surface of the sheet metal, often for decorative purposes.
Engraving: Engraving involves etching or cutting into the metal surface to create text, logos, or designs.
9. Finishing
Deburring: After cutting, metal edges may have burrs or sharp edges that need to be removed. Deburring processes smooth the edges for safety and aesthetics.
Polishing: Polishing improves the surface finish of the metal, giving it a smooth, shiny appearance. It can be done mechanically or through chemical processes.
Coating: Various coatings are applied to protect the sheet metal from corrosion or to improve its appearance. Common coatings include:
Powder Coating: A dry powder is applied electrostatically and then cured under heat to create a protective layer.
Galvanizing: A zinc coating is applied to protect the metal from rusting.
Anodizing: Mainly for aluminum, anodizing involves an electrolytic process that increases the thickness of the natural oxide layer for better corrosion resistance and aesthetic appeal.
Painting: Paints are applied to improve aesthetics and provide an additional layer of protection against corrosion.
10. Quality Control and Inspection
Inspections are carried out to ensure that the fabricated parts meet design specifications, tolerances, and quality standards. Non-destructive testing, dimensional checks, and visual inspections are commonly employed.
These sheet metal fabrication processes are used across various industries, including automotive, aerospace, construction, and electronics, to produce parts ranging from simple brackets to complex enclosures and structural components.
Click Sheet Metal Fabrication Companies in China or china sheet metal fabrication manufacturers to learn more about sheet metal fabrication services.
For all your electrical enclosures from China, contact china sheet metal fabrication companies-JIATONG now.
Sheet metal fabrication involves various processes to transform flat sheets of metal into desired shapes and components. These processes range from cutting and bending to assembling and finishing. Here are the main sheet metal fabrication processes: 1. Cutting Shearing: This is a basic cutting method where a sheet is cut into straight lines using shear…
Sheet metal fabrication involves various processes to transform flat sheets of metal into desired shapes and components. These processes range from cutting and bending to assembling and finishing. Here are the main sheet metal fabrication processes: 1. Cutting Shearing: This is a basic cutting method where a sheet is cut into straight lines using shear…