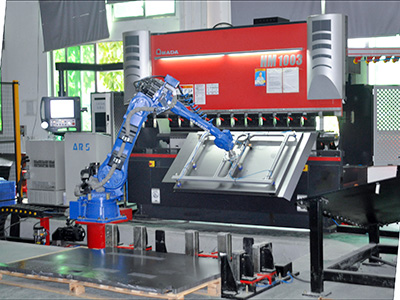
Some bending methods
-
by Yan yifan
- 380
1)Suspended bending (also called three-point bending)
The punch presses the workpiece into the die without pressing it against the die wall. When the punch core moves down, the edge of the workpiece bends upward and forms an included angle. The deeper the punch presses the workpiece into the die, the smaller the angle. At this time, there is a gap between the punch core and the die. Hanging bending is also called path dependent process. Each angle requires a specific path. The machine tool control system calculates the path and the corresponding impulse pressure at the same time. The path and punching force depend on the mold, material and product characteristics (included angle, length).
2)Bending in die (also called bottom bending)
The punch core completely presses the workpiece into the die, so there is no gap between the die, the workpiece and the punch core. This process is called clamping. The punch core and die must fit each other accurately. Therefore, each included angle and shape requires corresponding die components. Once the workpiece is fully pressed in, the punch core cannot continue to move downward. The machine tool control system continues to raise the impulse pressure until it reaches the specified value. The pressure applied to the workpiece thus rises, showing the contour of the punch and die. The included angle is gradually stabilized under the action of high pressure, and the rebound problem is almost completely eliminated.
3)Flap bending
The built-in bending swing arm of the machine tool is composed of C-shaped profiles, on which the lower and upper bending dies are installed. During bending, the C-shaped profile moves upward or downward, or performs a small-scale elliptical movement. The semi-automatic operation of the swing arm bending machine is famous for its rapidity and flexibility. Even small batch production is not inferior. In addition, the first mock exam can also achieve the efficient bending of various radius dimensions on the single die by using the same die.
4)Folding and pressing (combined bending)
The edges of the sheet are usually fully bent (e.g. box edges) and then folded parallel to each other. The finished product is therefore more stable as a whole or forms edge protection. Then, other parts usually need to be hung in the hem. Folding and pressing are completed in two steps: first, the operator folds the included angle of 30 ° in advance, and then puts the workpiece back in and presses the included angle.
1)Suspended bending (also called three-point bending) The punch presses the workpiece into the die without pressing it against the die wall. When the punch core moves down, the edge of the workpiece bends upward and forms an included angle. The deeper the punch presses the workpiece into the die, the smaller the angle. At this…
1)Suspended bending (also called three-point bending) The punch presses the workpiece into the die without pressing it against the die wall. When the punch core moves down, the edge of the workpiece bends upward and forms an included angle. The deeper the punch presses the workpiece into the die, the smaller the angle. At this…