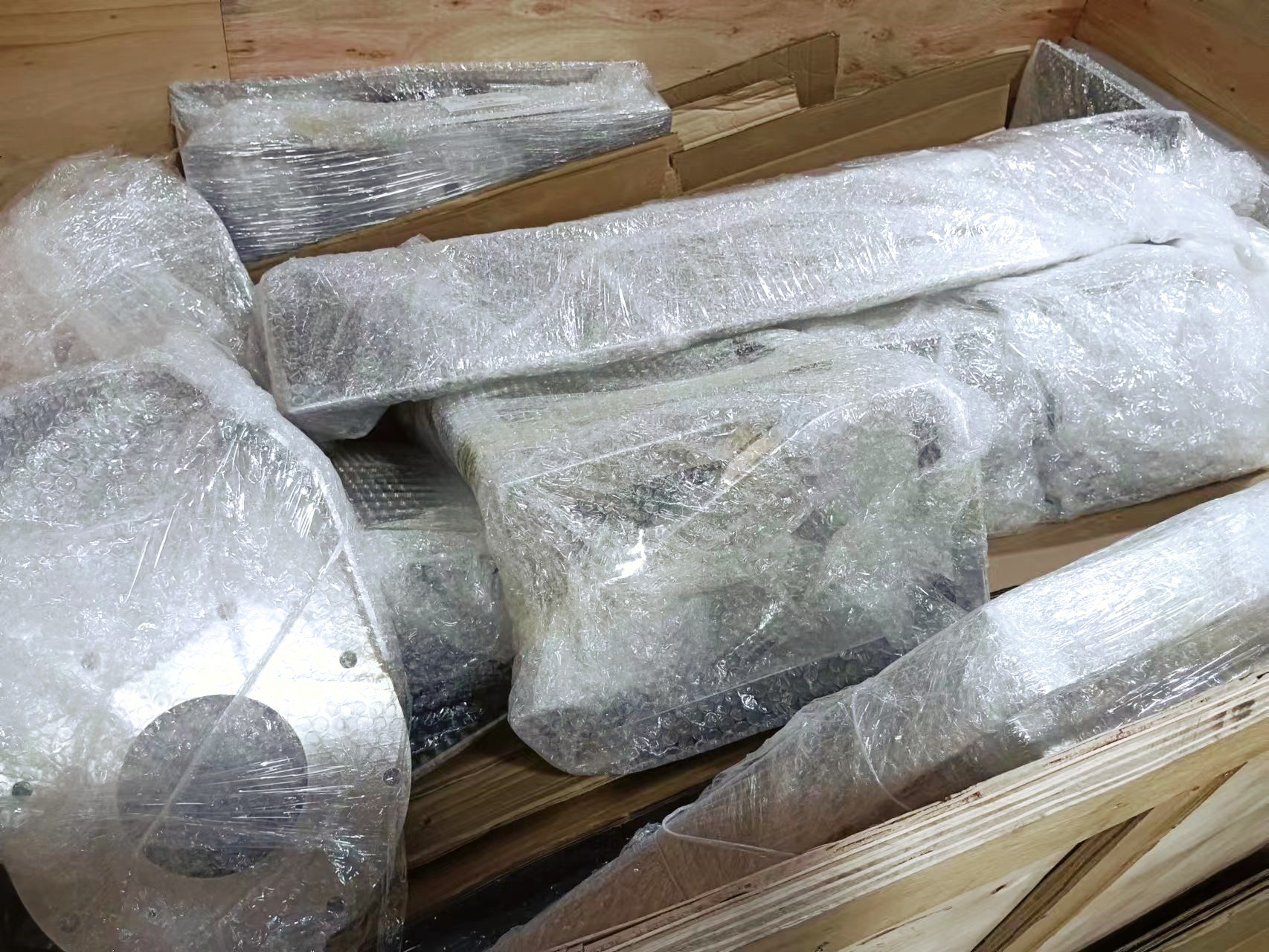
What are the steps in sheet metal fabrication?
-
by Jiatong
- 294
1. Design and Engineering
- Concept and Planning: The first step is to understand the requirements and create a concept for the final product.
- CAD Design: A detailed design is created using computer-aided design (CAD) software. This includes precise measurements and specifications.
2. Material Selection
- Choosing the appropriate type of metal based on the project’s requirements, such as strength, durability, weight, and resistance to corrosion.
3. Cutting
- Shearing: A process that involves cutting large sheets into smaller, more manageable pieces.
- Laser Cutting: A high-precision method that uses a laser to cut intricate shapes and designs.
- Waterjet Cutting: Uses a high-pressure stream of water mixed with abrasive particles to cut through metal.
- Plasma Cutting: Uses an electrically conductive gas to transfer energy from a power supply to any conductive material, effectively cutting through it.
4. Forming
- Bending: The metal sheet is bent into the desired shape using press brakes or other bending tools.
- Rolling: The metal is passed through a set of rolls to form cylindrical or curved shapes.
- Stamping: A process where a metal sheet is placed in a press and shaped using a die and punch.
5. Joining
- Welding: Joining two or more pieces of metal using heat and filler material.
- Riveting: A mechanical fastener is used to join sheets together.
- Adhesives: Sometimes adhesives are used to bond metal parts together.
6. Finishing
- Deburring: Removing sharp edges or burrs from the cut metal.
- Polishing: Smoothing the surface to improve appearance and remove imperfections.
- Coating: Applying a protective layer, such as paint, powder coating, or anodizing, to enhance durability and appearance.
7. Assembly
- The individual fabricated parts are assembled into the final product, which may include additional processes such as hardware installation or final adjustments.
8. Quality Control
- Inspection and testing to ensure that the fabricated product meets the required specifications and standards.
9. Packaging and Delivery
- The final product is packaged and prepared for delivery to the customer.
These steps can be adapted or expanded depending on the specific requirements of the project and the type of metal being fabricated. Each step requires specialized equipment and skilled technicians to ensure the final product meets the desired quality and specifications.
Related Links:
china custom sheet metal parts | sheet metal fabrication company china | china sheet metal fabrication companies | china sheet metal fabrication manufacturers | china sheet metal forming manufacturers | china sheet metal fabrication factory | sheet metal fabrication companies in china | sheet metal parts manufacturing china | china sheet metal parts manufacturers | china sheet metal parts company | china metal enclosure manufacturers | china aluminum sheet metal fabrication manufacturers | china sheet metal manufacturing manufacturers
Sheet metal fabrication involves a series of processes that transform flat sheets of metal into desired shapes and products. The steps can vary depending on the complexity of the project and the type of metal being used, but the general process typically includes the following: 1. Design and Engineering Concept and Planning: The first step…
Sheet metal fabrication involves a series of processes that transform flat sheets of metal into desired shapes and products. The steps can vary depending on the complexity of the project and the type of metal being used, but the general process typically includes the following: 1. Design and Engineering Concept and Planning: The first step…